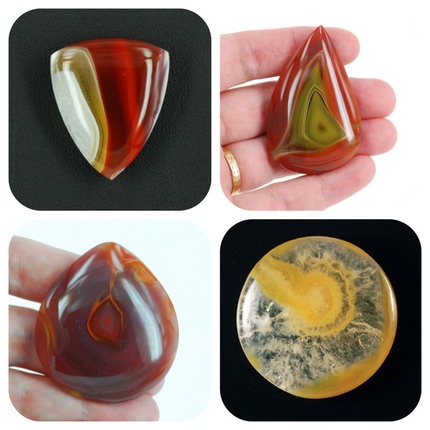
The reason I started making jewellery was to have some way to showcase the beautiful rocks that were becoming an obsession, verging on needing intervention. I was entirely not content to leave them in a dusty display case where only myself, my family and the occasional visitor silly enough to express a vague interest could see them. Living in Queensland, Australia, I have access to 'rough' of one of the most beautiful agates in the world - Queensland Agate. This agate is terribly originally named - it comes from Agate Creek in Queensland, and I live approximately 1740 odd kilometres away. I'm virtually sitting right on top of it ;). The above collage is of some of the Queensland agate cabochons that have been cut either by me, my husband or my father. We all admit to the same obsession, so sadly there's no-one to implement an intervention on our behalf. It's probably too late for us all anyway!
I thought I'd give a little peek of my process from rough start to polished finish. I have a house full of equipment, with lapidary equipment out the back for the cutting of the rocks, to my own little room in the front full of awesome tools and some fire to create the setting.
So let's start at the very beginning: a very good place to start! As I have two small children, rockhounding into the middle of Australia (unbearable heat, dirt and oh, so much whinging... not to mention no toilets or showers) isn't really do-able at this point in my life. So I frequent rock and gem shows to pick up whatever rough the local grizzled rockhounds are willing to part with.
PART 1 - FROM ROUGH ROCK TO SHINY CABOCHON
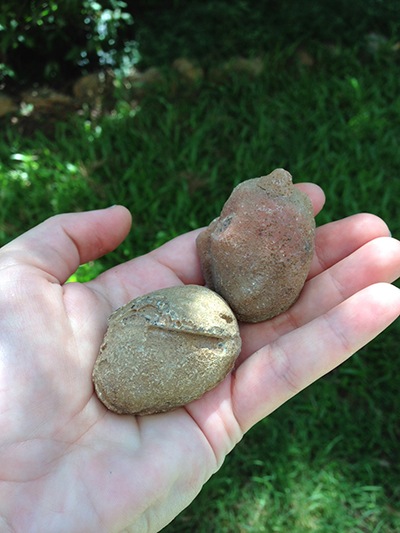
These are a couple of pieces of Queensland Agate, just as they come from the ground. Possibly a little cleaner. Innocent looking pebbles, aren't they? Who knows what beauty dwells within? Well, no-one, until we get these fellas on the slab saw.

The slab saw will cut a slice through this agate to reveal what is hiding inside. Not every rock has a useable inside - big areas of bland quartz, blah colours and unattractive inclusions makes this part of the process time consuming and a LOT of rough needs to be cut before you might chance on a pretty piece, with strong, interesting, clean patterning and/or colouring. And then, a fracture line across the face can render the whole thing useless, and break a lapidarist's heart.

Well, looky here! This one has surely got something purty going on inside. Let's cut it again so that we have a slice with two flat sides - front and back. I'm going to fully admit that this was the 8th pebble that I cut - the first 7 were rubbish. It's all the luck of the draw. Also, please excuse my awful-looking-car-door-battered thumbnail in all of the shots.
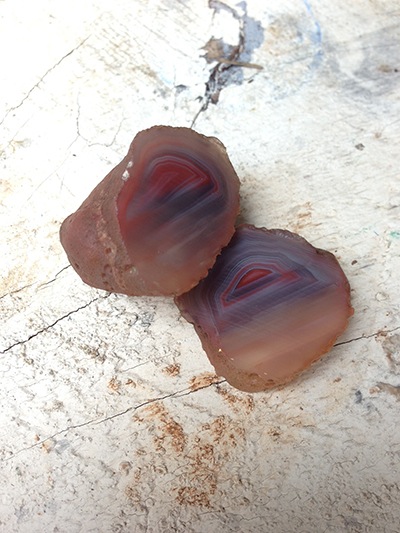
Here's the resulting slice. It's not a stunner, but it's a pretty example of some of the dove gray/red material. There are so many colours in Queensland Agate, I'll share some of them with you in later posts.
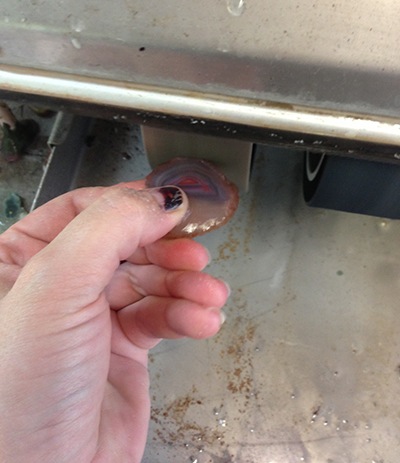
Onto the grinding wheel it goes, to take the rind off the outside and see what's left when that's gone. Then, I generally decide on a freeform shape, whatever best suits the pattern in the stone.
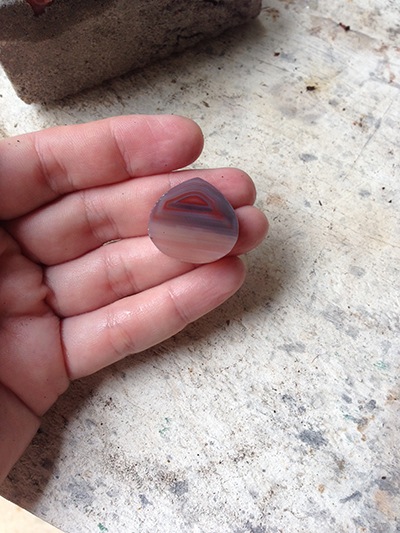
With the rind gone, a teardrop shape appeared. Here's the pre-form, ready to be dopped, domed and polished.
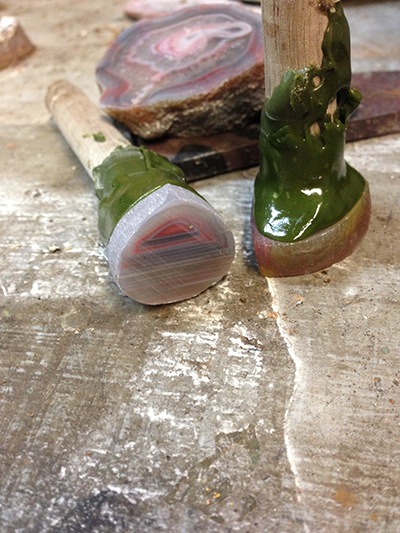
The pre-form is dopped - attached to a stick with wax. This is to help hold the piece while it's being shaped and polished on the grinding wheels. My dad domes his cabochons without dopping them!?! I have no idea how he doesn't take off all his fingertips!
Now, gotta wait until that wax cools right down. Time for a coffee break…..
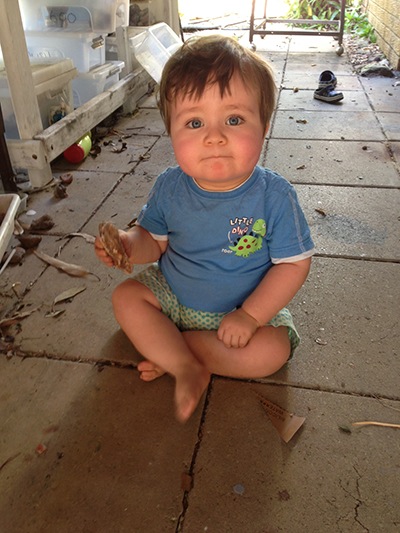
……. *sip sip* Here's a picture of one of my little helpers. He's very patient, helps me sort the rocks and always gives them the taste test of approval before moving onto the next one.
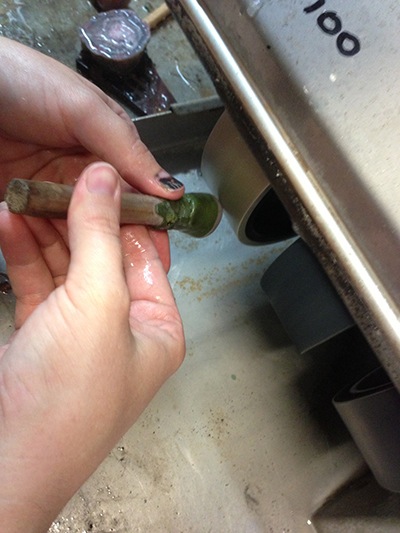
Slurp, coffee's done. Time to shape the dome of the cab (cabochon), moving progressively through grits from rough (100) to super-fine (3000). There's water dripping on those wheels to help lubricate the process and to prevent the stone from getting too hot.
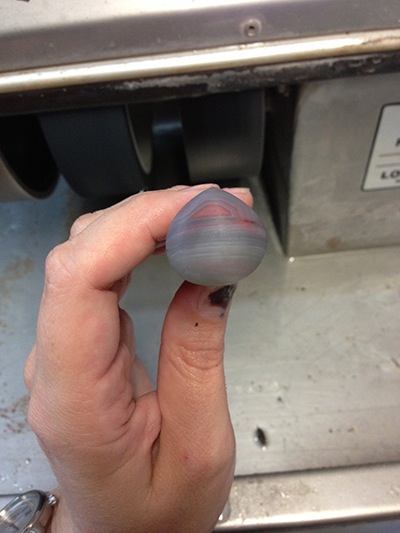
Here's the cab after the 280 grit - formed and generally smoothed. Now to move through 600, 1200 and 3000……
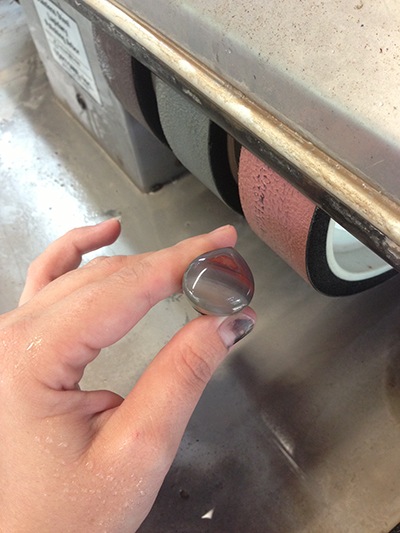
After the 3000 grit wheel, the cab is pre-polished and, because it's agate and super-hard, it's already got a pretty great shine. But that's nothing compared to what it will look like after the final polish.
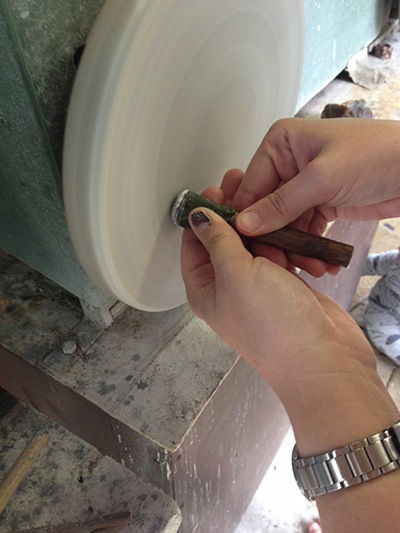
The final polish happens on a wet leather flat wheel, charged with tin oxide. There are heaps of different ways that lapidarists achieve this final polish, but this way works really well for me, especially on hard stones like agate. It gives the agate an absolutely glass-like finish, like the gloss has been poured on! This is one of the reasons that I simply adore Queensland Agate - I am quite partial to delicious shiny sparkly things. :D

And here we are, the tin oxide and leather have done their job, and this agate is buffed to shiny deliciousness. Now, how do we get this rock off this darn wax so that I can turn it into something pretty to wear?

Into the freezer it goes (hmm, might be time to throw away those frostbitten leftovers), and then, when it's cold enough……..
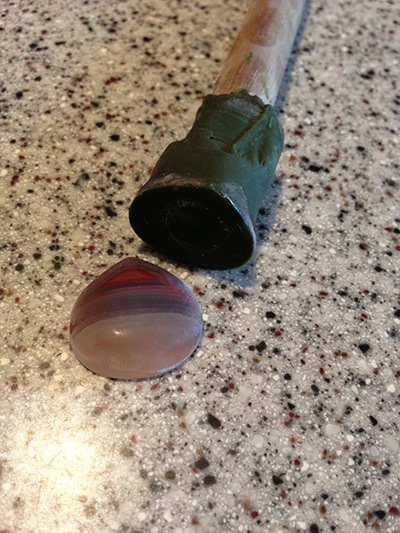
……..POP! Off the wax it comes, complete with frosty rime.
Now, even though it's shiny and gorgeous, the rock is still not ready to be set.
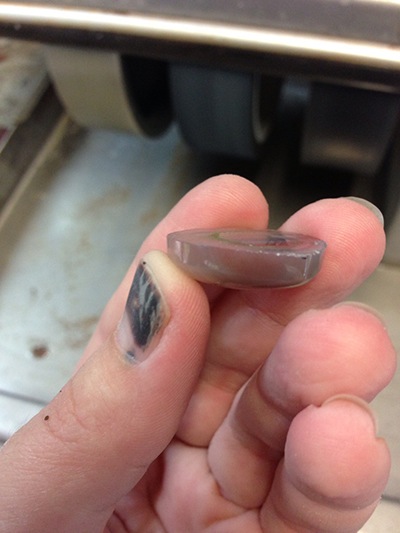
The front and sides are shiny and smooth, but the back edge is really rough and sharp, and this will make popping the stone in and out while setting really tricky. It can prevent the stone from sitting well in the setting too. Plus, it feels yucky in the hand and makes an ugly finish, so let's knock that off. Back on the grinding wheel it goes - champfer that sharp arris off of the back edge!
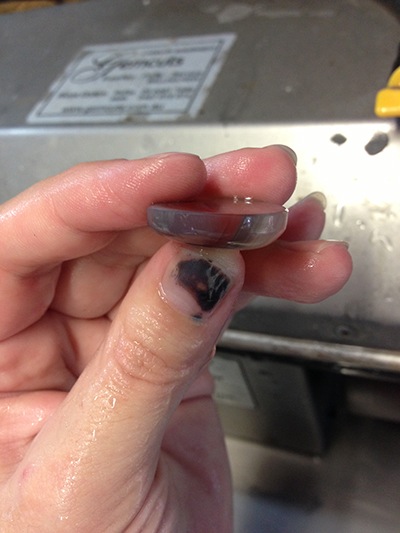
There, now it's lovely to touch. I also gave the back a quick polish - it won't be seen when the stone is set, but I'll know it's there. ;)
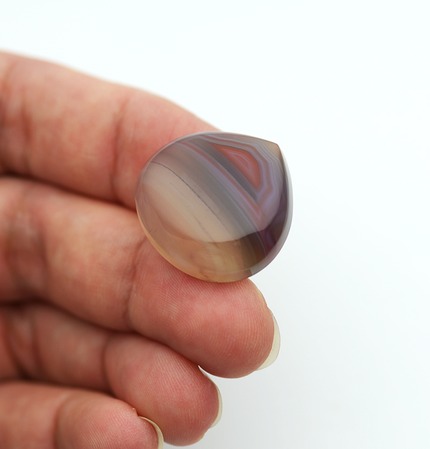
And, TA DA! A cabochon of Queensland agate, ready to be turned into a one-of-a-kind piece of jewellery. And no matter how simple the setting, every piece made with a handcut rock is unique, because no two rocks are the same!
Wanna see what comes next? Then click….
Part 2…..FROM SHINY ROCK TO WEARABLE ART.
El x
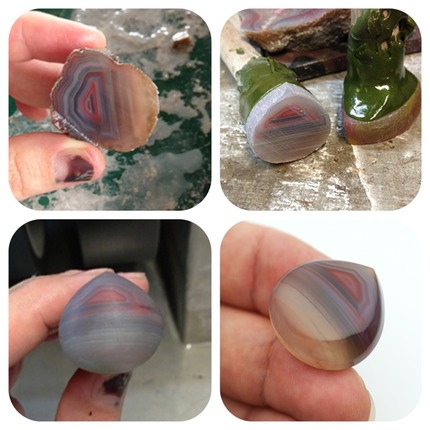